- Assembly Process
-
Cathode and anode electrode sheets, completed through the electrode process, are assembled into battery cells by integrating them with other key battery components: separators and electrolytes.
The Assembly process may vary depending on the battery cell's form factor and the manufacturer's technology.
- Prismatic Cell
-
Prismatic batteries are renowned for their exceptional structural safety.
Their robust form factor ensures high resistance to physical damage, even in the event of collisions or external impacts.
Additionally, prismatic batteries efficiently dissipate heat generated internally during operation, which is crucial for preventing performance degradation and extending battery lifespan.

- Foil Pre Welding
- cap-cc laser welding
- jr insert
- SEAM WELDING
- el filling
- sealing
- Foil Pre-Welding Equipment
- The Foil Pre-Welding Equipment utilizes ultrasonic welding to join foil and tab components of jelly-rolled cathode and anode sheets, ensuring strong and reliable connections essential for battery performance.
- FOIL PRE WELDING
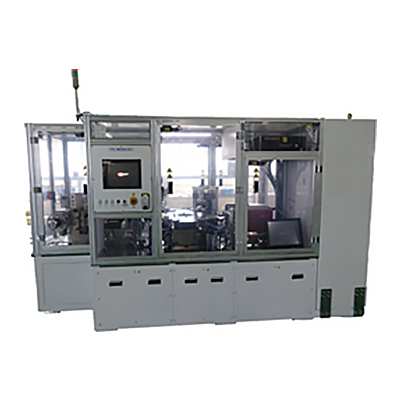
Features and Advantages
Integrated Ultrasonic Welding, Cutting, and Inspection Our Pre-Welding System combines ultrasonic welding, cutting, and inspection processes in a single equipment, optimizing space utilization. Precision Electrode Alignment ensures minimal welding defects through meticulous alignment of electrode sheet. Customizable Welding Configurations providing flexibility in production.
- 01Equipment Specifications
-
Machine Size : 13m(W) x 2.5m(L) x 2.2m(H)
Cell Size : 100x250mm(W), 250x600mm(L), 25mm(T)
Pre Welding : Ultrasonic
- 02Key Functions
-
Ultrasonic Welding
Simultaneous Electrode Alignment and Welding
Dust and Particle Minimization using suction and blower systems.
Air Cooling Structure for Welding unit.
Integrated welding, cutting, and inspection into a unified process.
Main PLC Control and MES Integration
- Laser Cap-CC Welding Equipment
-
The Laser Cap-CC Welding Equipment is designed to join Caps and CCs or Foils and CCs using laser technology,
ensuring precise and strong welds essential for battery performance.
- Laser Cap-CC Welding Equipment
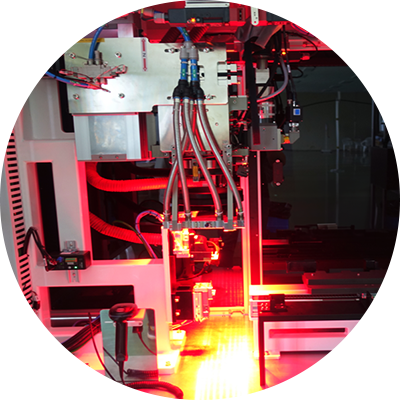
Features and Advantages
Features and Advantages
High Accuracy and Weld Strength
Achieves exceptional precision and robust weld strength
Compatible with versatile Welding Methods, including spot, line, and wobble
Rapid Welding utilizing Scanner Heads
Flexible Structural configurations tailored to specific process needs
- 01Equipment Specifications
-
Machine Size : 3.5m(W) x 7.5m(L) x 2.5m(H)
Cell Size : 100x250mm(W), 250x600mm(L), 25x60mm(T)
Welding : Laser(Fiber 2~5kw)
- 02Key Functions
-
Scanner Head with maximum 240x240mm coverage
Optimal welding quality utilizing stable shielding gas supply and dust collection during welding
Safety-Enhanced Laser operation incorporating internal and external shielding
Centralized PLC control and seamless integration MES
- JR Insert Equipment
- The JR Insert Equipment is to align JR to the can inlet and insert them accurately into the designated position.
- JR INSERT
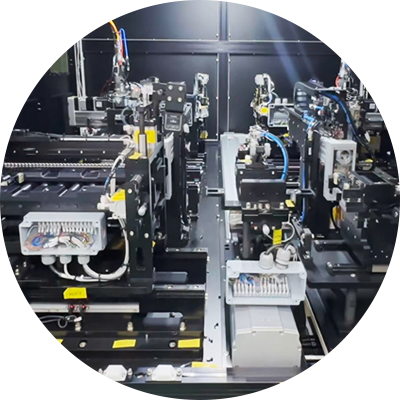
Features and Advantages
Unique insertion technique minimizing damage to JR during insertion.
Adaptable Processing for Different Can Shapes
Integrated Cleaning, Inserting, and Inspection processes within a single system
Seamlessly incorporated laser welding according to specific requirements.
- 01Equipment Specifications
-
Machine Size : 3m(W) x 8m(L) x 2.2m(H)
Cell Size : 100x250mm(W), 250x600mm(L), 25x60mm(T)
- 02Key Functions
-
Integrated Cleaning, Vision Inspection, Inserting, and Welding
Combines Can cleaning, vision inspection, inserting, and welding into a unified process.
Stable alignment structure minimizing damage to JR
Precise control & adjustment utilizing Pressure sensors
Centralized PLC Control and Seamless MES Integration
- Seam Welding Equipment
- The Seam Welding Equipment seals JR-inserted-Can and Lid and using laser welding technology.
- SEAM WELDING
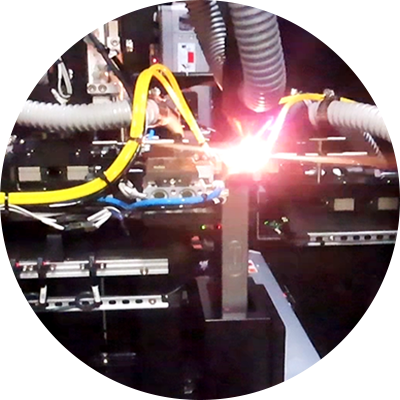
Features and Advantages
Perfect welding for complete airtight seals.
Adaptable processes based on various Can configurations.
Integrated shielding gas supply and dust collection for optimal welding quality.
Customized Welding Recipes by Specification
- 01Equipment Specifications
-
Machine Size : 14m(W) x 12m(L) x 2.5m(H)
Cell Size : 100x250mm(W), 250x600mm(L), 25x60mm(T)
Welding : Laser(Fiber 2~8kw)
- 02Key Functions
-
Stable alignment structure for optimal welding results
Optimal welding recipes application
Combines welding processes into a unified system, simplifying operations.
Centralized PLC Control and Seamless MES Integration
- EL Filling Equipment
- The EL Filling Equipment injects electrolyte into sealed cells.
- EL FILLING
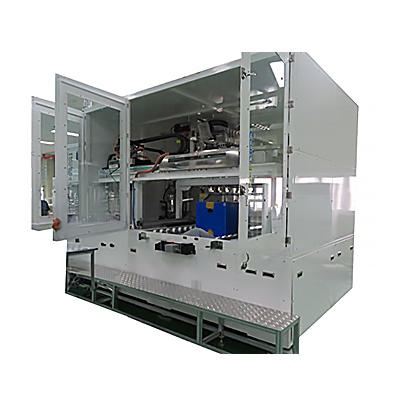
Features and Advantages
Hopper Vacuum Structure for Reduced Filling Time
Dripping-Proof Structure Preventing Any Leakage During Cell Transport
Precise Electrolyte Injection
Compact Structure
- 01Equipment Specifications
-
Machine Size : 14m(W) x 10m(L) x 3m(H)
Cell Size : 100x250mm(W), 250x600mm(L), 25x60mm(T)
Electrolyte Filling Capacity: Max 1200g
- 02Key Functions
-
Individual Cell Vacuum Management
High-Speed Electrolyte Filling for Optimized Speed
A More Stable Configuration Compared to Traditional Vacuum Chamber Techniques
Centralized PLC Control and Seamless MES Integration
- Sealing Equipment
- The Sealing Equipment fully seals the electrolyte injection port of the cell, producing a completed cell.
- SEALING
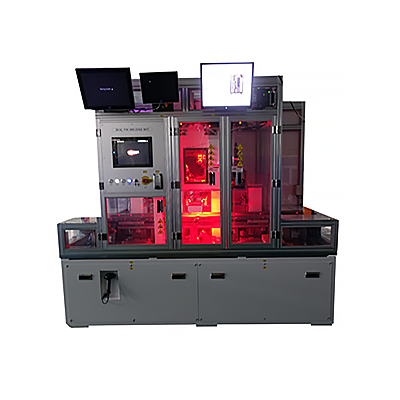
Features and Advantages
Rapid Welding Utilizing Scanner Heads
Integrated Structure for Seal Cover Feeding, Cleaning, Laser Welding, and Inspection
High Welding Accuracy through Automatic Position Correction
Electrolyte Leakage Prevention and Explosion-Proof Design
- 01Equipment Specifications
-
Machine Size : 12m(W) x 3m(L) x 3m(H)
Cell Size : 100x250mm(W), 250x600mm(L), 25x60mm(T)
Welding : Laser(Fiber 2~3kw)
- 02Key Functions
-
Laser Cleaning Structure Applied (Optional)
Optimal welding quality by utilizing a stable shielding gas supply and dust collection system during welding.
Safety-Enhanced Laser Operation Incorporates internal and external shielding to create a safe laser working environment.
Centralized PLC Control and Seamless MES Integration
High Speed Sealing