- Assembly Process
-
Cathode and anode electrode sheets, completed through the electrode process, are assembled into battery cells by integrating them with other key battery components: separators and electrolytes.
The Assembly process may vary depending on the battery cell's form factor and the manufacturer's technology.
- Pouch Cell
-
Pouch-type cells are batteries that contain liquid electrolyte within soft packaging materials.
They are lightweight and flexible, and they provide the advantage of relatively low heat generation.

- NOTCHING SYSTEM
- CUTTING SYSTEM
- STACKING SYSTEM
- TAB WELDING SYSTEM
- PACKAGING SYSTEM
- DEGASSING SYSTEM
- Notching Equipment
-
Our Notching Equipment utilizes laser and mold presses to shape and cut the tab areas of electrode reels,
transforming them into reel or sheet form with precision and efficiency.
- NOTCHING SYSTEM

Features and Advantages
Top Performance Speed mPLUS's roll-to-sheet notching technology delivers the world's fastest production speeds, ensuring unmatched performance in the industry.
Maximized Production Efficiency Our innovative magazine change solution enables seamless production without equipment stoppages, significantly enhancing overall manufacturing efficiency.
- 01Equipment Specifications
-
Machine size : 9.6m(L) x 3m(W) x 2.6m(H)
- Turret unwinder typeWeb diameter : Max. 800mm (Space. ø900)
Sheet width : Max. 200mm
Length : Max. 700mm
- 02Key Functions
-
Dual/Single Winder Method
Laser/Mold Notching System
Real-Time Vision-Based Inspection
Suction and cleaning system minimizing dust and particles during electrode transport.
Movable touch panel enhancing operator convenience with accessibility for smooth unit operation.
Automatic electrode and magazine exchange applied, maximizing productivity by enabling automatic electrode swaps and magazine changes without halting equipment, ensuring continuous production.
- Cutting Equipment
- The Cutting Equipment performs slicing electrode reels that have undergone tab forming into precise sheet forms.
- CUTTING SYSTEM
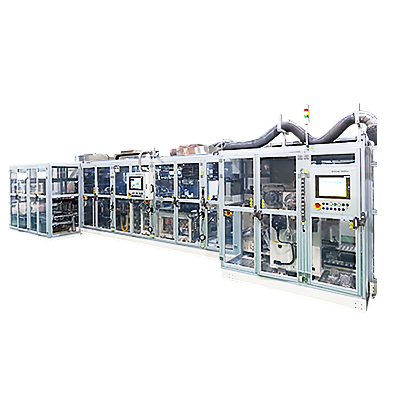
Features and Advantages
Top Performance Speed mPLUS's roll-to-sheet electrode cutting method delivers the world's highest production speeds, ensuring superior performance and productivity.
Maximized Production Efficiency Our innovative magazine change system enables continuous production without equipment stoppages, significantly enhancing overall manufacturing efficiency.
- 01Equipment Specifications
-
Machine size : 8.4m(L) x 3m(W) x 2.6m(H)
- Turret unwinder typeWeb diameter : Max. 800mm (Space. ø900)
Sheet width : Max. 200mm
Length : Max. 700mm
- 02Key Functions
-
Dual/Single Winder
Provides flexibility in winding operations to accommodate different production needs.
Tab Guide & Taper Roller preventing electrode tab folding during transport Automatic Feeding & Cutting Position Correction by distance measurement between tab pitches.
Real-Time Electrode Dimension & Surface Inspection utilizing Vision
Suction & Cleaning system minimizing dust and particles to key areas during electrode transport.
Automatic Electrode and Magazine Exchange maximizing productivity by enabling automatic electrode swaps and magazine changes without halting equipment, ensuring continuous production.
- Stacking Equipment
- The Stacking Equipment performs the crucial process of layering electrode sheets into a Jelly Roll configuration.
- STACKING SYSTEM
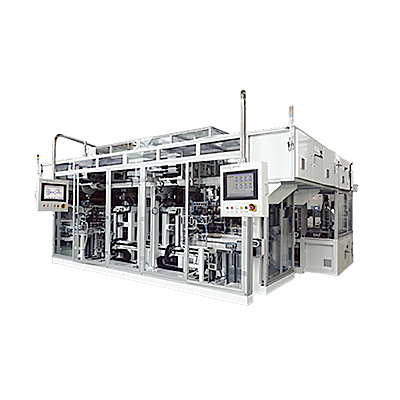
Features and Advantages
World-Class Performance and Stacking Quality mPLUS's stacking system employs advanced stacking methods to achieve industry-leading stacking speeds and exceptional quality.
Versatile Compatibility Capable of accommodating both unidirectional and bidirectional Tab designs.
- 01Equipment Specifications
-
Sheet width : Max. 130mm
Length : Max. 600mm
- 02Key Functions
-
Precision Separator Tension Control
High-Speed Stacking System
Intuitive High-Speed Electrode Alignment and Inspection
High-Speed Double-Stacked Sheets Separation System
Automatic Electrode and Separator Exchange Without Halting Equipment
Support for Various Separator Finishing Options (Taping, Bonding, and Heat Pressing)
- Tab Welding Equipment
-
The Tab Welding Equipment welds foil and tab components,
which collect current from multiple stacked electrode sheets, into a single point.
- TAB WELDING SYSTEM
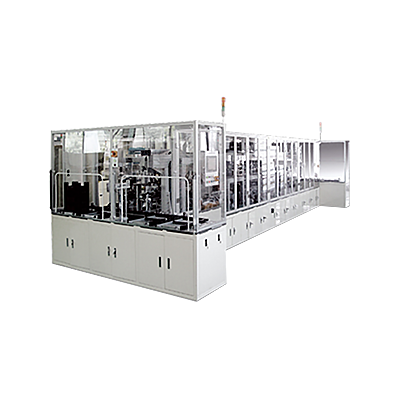
Features and Advantages
Industry-Leading Performance Speed mPLUS's Tab Welding System delivers the world's fastest welding speeds, ensuring unmatched performance and productivity.
Versatile Compatibility Our Tab Welding System is designed to accommodate both unidirectional and bidirectional Tab designs.
- 01Equipment Specifications
-
Machine Size : 17m(W) x 2,2m(L) x 2.2m(H)
Cell Size : 80x150mm(W), 200x600mm(L), 15mm(T)
Tab Welding : Laser
- 02Key Functions
-
Dual/Single Direction Tab Compatibility Enables versatile model capabilities.
Real-Time Vision Inspection
Ultrasonic Welding ensuring precise and rapid welding performance.
Barcode Labeling System facilitating traceability management of each product.
- Packaging Equipment
-
The Packaging Equipment shapes battery cells by wrapping them in pouches,
injecting electrolyte, and sealing them before discharge.
- PACKAGING SYSTEM
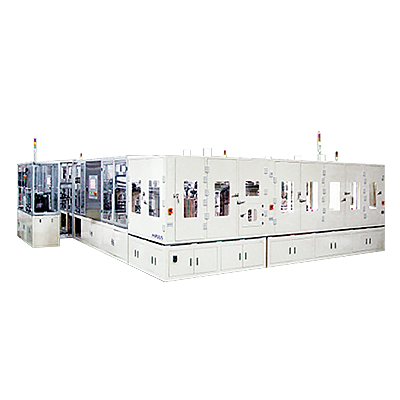
Features and Advantages
Industry-Leading Performance Speed mPLUS's Packaging System delivers the world's fastest processing speeds, establishing it as the premier choice in packaging equipment.
Versatile Equipment Compatibility Our Packaging System can be independently installed for forming, sealing, and electrolyte filling, allowing flexible adaptation to meet diverse installation site requirements.
- 01Equipment Specifications
-
Machine Size : 30m(W) x 10m(L) x 2.5m(H)
Cell Size : 80x150mm(W), 200x600mm(L), 15mm(T)
Electrolyte Filling Capacity: Max 600g
- 02Key Functions
-
Uniformed Pouch Forming Quality utilizing temperature compensation system
High-Capacity, High-Speed Electrolyte Filling maximizing production efficiency and preventing cell contamination
Leak Minimization by utilizing high-performance vacuum pumps and sealed chambers
Real-Time Vision Inspection
High-Speed Electrolyte Filling System utilizing Fill tubes
High Speed and Temperature Stabilization
- Degassing Equipment
- The Degassing Equipment removes gaseous impurities generated internally after the initial charging and discharging cycles, completing the final shape of the battery cell.
- DEGASSING SYSTEM
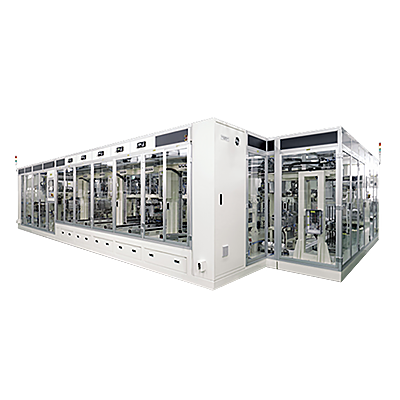
Features and Advantages
Integrated Functionality System mPLUS's Degassing System combines battery rolling functions and inspection equipment within a single setup, maximizing efficiency through its multifunctional capabilities.
Convenient Maintenance Designed with a four-sided access mechanism, our system facilitates easy maintenance. Additionally, the top-opening vacuum chamber design enhances the convenience of chamber maintenance.
- 01Equipment Specifications
-
Machine Size : 20m(W) x 10m(L) x 2.5m(H)
Cell Size : 80x150mm(W), 200x600mm(L), 15mm(T)
- 02Key Functions
-
Single/Double Folding option allowing various battery cell configuration acceptance.
Simultaneous Loading and Unloading of Battery Trays and Cells enhancing operational convenience.
Easy Model Changes through minimal part exchanges.
Real-Time Vision Inspection
Piercing System for Minimizing Contamination in Vacuum Chambers